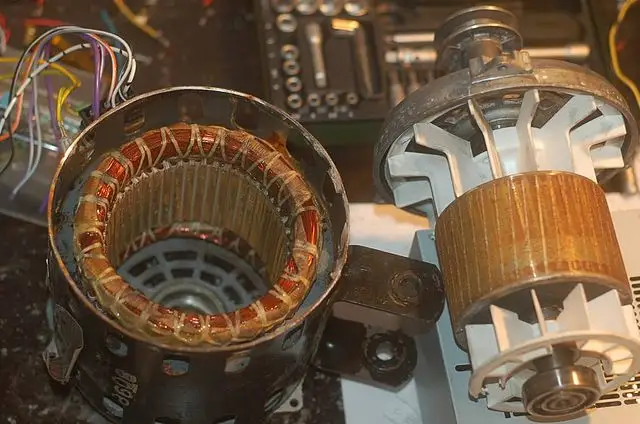
Squirrel Cage Motor: An Overview
What is a Squirrel Cage Induction Motor?
A squirrel cage induction motor is a strong and popular asynchronous AC motor. The rotor is designed to look like a squirrel cage, and it contains conductive bars in a laminated iron core. This allows the motor to operate using electromagnetic induction.
When alternating current is supplied to the stator windings, it generates a rotating magnetic field. This field induces currents within the rotor bars that generate a secondary magnetic field. The interaction between these magnetic fields generates torque and causes the rotor to rotate.
Squirrel cage induction motors are the preferred choice for applications requiring constant speed operation, such as driving industrial equipment like pumps, fans, and conveyors. Their durability, cost-effectiveness, minimal maintenance requirements, and high efficiency in energy conversion make them the obvious choice. Furthermore, the ability to customize speed-torque characteristics by modifying rotor bar shapes makes these motors adaptable to a variety of operational demands.
Squirrel Cage Induction Motor Working Principle
The operational principle of a squirrel cage induction motor is based on the interaction of magnetic fields within the motor. The application of a three-phase AC voltage to the stator windings establishes a rotating magnetic field. This field induces a voltage in the rotor bars, allowing currents to flow through them. These rotor currents generate their own magnetic field, which interacts with the stator field to produce a torque that causes the rotor to follow the rotating magnetic field.
The rotor never quite reaches the synchronous speed of the rotating magnetic field. This difference in speed, known as "slip," is necessary to maintain the induction process. As the rotor accelerates, and the relative motion between the rotor and the stator field decreases, the induced current and torque also diminish. This deceleration re-establishes the relative motion, ensuring continuous induction and rotation. The slip frequency, which is the difference between the synchronous speed and the rotor speed, determines the frequency of the induced rotor currents.
Squirrel Cage Induction Motor Construction
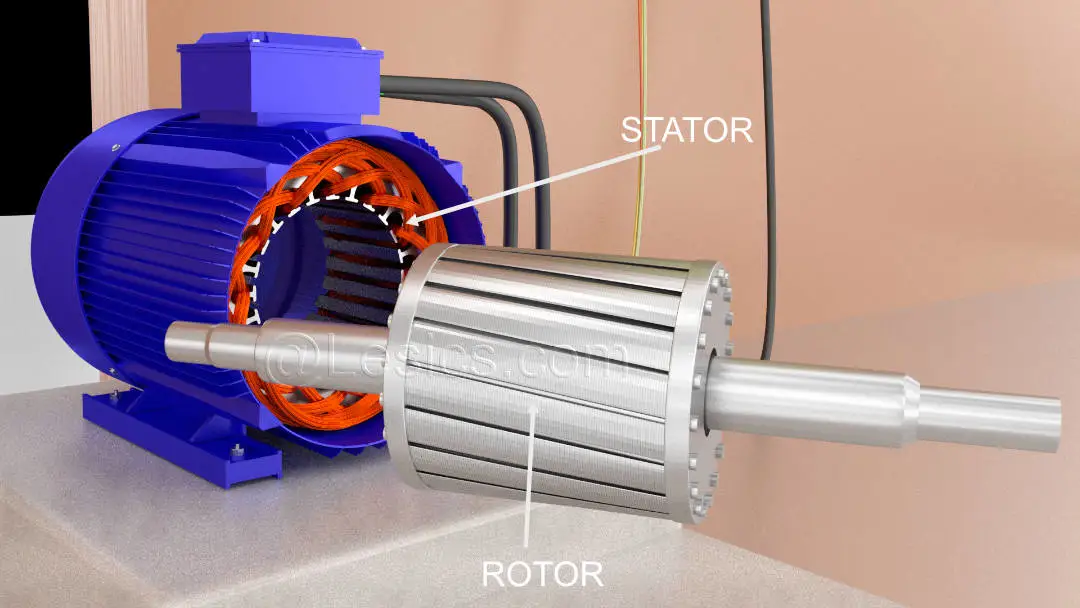
Stator
The stator is the stationary part of the motor, housing the three-phase windings responsible for generating the rotating magnetic field. These windings are typically spaced 120 degrees apart, both electrically and mechanically. The stator core, constructed from laminated iron, provides a low-reluctance path for the magnetic flux, enhancing the efficiency of magnetic field generation.
Rotor
The rotor is the rotating component of the motor, efficiently converting electrical energy into mechanical energy. It consists of a laminated iron core with embedded conductive bars, typically made of copper or aluminum, forming the distinctive "squirrel cage" structure. The rotor core laminations are important for minimizing eddy current losses.
Fan and Bearings
A fan, typically attached to the non-drive end of the rotor shaft, provides heat dissipation, ensuring operation within safe temperature limits. High-quality bearings, supporting the rotor shaft, enable smooth and efficient rotation.
Applications of Squirrel Cage Induction Motor
Squirrel cage induction motors are widely used across a broad range of industrial sectors due to their inherent advantages of constant speed operation, self-starting capability, and low maintenance needs. They are commonly found in applications such as: driving centrifugal pumps for fluid transportation; powering industrial drives, including conveyor belts for material handling; operating large blowers and fans for ventilation and air circulation; driving machine tools in manufacturing processes; and powering lathes and other turning equipment for metalworking operations.
Advantages and Disadvantages of Squirrel Cage Induction Motor
Squirrel cage induction motors offer numerous advantages that contribute to their widespread adoption. Their cost-effectiveness, stemming from a relatively simple design, results in lower manufacturing costs compared to other motor types. Reduced maintenance is another key benefit; the absence of slip rings and brushes eliminates the need for their associated upkeep. Good speed regulation is a defining characteristic, as they maintain a relatively constant speed under varying load conditions. Their high efficiency in energy conversion is notable. Effective heat regulation is ensured by the integrated fan, preventing overheating. Their design allows for a compact and lightweight structure, facilitating integration into various systems. Finally, the absence of sparking components makes them suitable for hazardous environments.
However, despite their numerous merits, squirrel cage induction motors also possess certain limitations. Their speed control capabilities are limited, necessitating external control mechanisms for variable speed applications. They typically draw a high current during startup, which can pose challenges for power systems. Their performance can be affected by voltage fluctuations in the power supply.
Difference Between Squirrel Cage and Slip Ring Induction Motor
While both squirrel cage and slip ring induction motors operate on the principle of electromagnetic induction, they differ in their rotor construction and operational characteristics.
Unlike the squirrel cage rotor with its short-circuited bars, a slip ring induction motor employs a wound rotor with external connections via slip rings and brushes. This design allows for the introduction of external resistance into the rotor circuit, providing greater control over the motor's starting torque, starting current, and speed. By adjusting the external resistance, the starting current can be reduced, the starting torque can be increased, and the speed can be adjusted to meet specific application requirements. Furthermore, slip ring motors generally exhibit a better power factor compared to squirrel cage motors, particularly at lower speeds. However, these advantages come at the cost of increased complexity and maintenance. The presence of slip rings and brushes requires regular maintenance and periodic replacement, adding to the overall operational costs. Moreover, the introduction of external resistance in the rotor circuit leads to higher power losses, resulting in lower efficiency compared to squirrel cage motors.
Classification of Squirrel Cage Induction Motor
Recognizing the diverse performance characteristics of squirrel cage induction motors, organizations like NEMA (National Electrical Manufacturer's Association) and IEC (International Electrotechnical Commission) have established classification systems based on speed-torque characteristics. These classifications, ranging from Class A to Class F, provide a standardized framework for categorizing motors based on their starting torque, starting current, and slip characteristics.
NEMA Classifications
NEMA classifications primarily focus on the starting torque and current characteristics of the motor. This categorization aids in the selection of appropriate motors for specific applications, particularly considering the impact of motor startup on power systems.
Squirrel cage motor Class A exhibits standard starting torque and current values with low slip, typically less than 5%. The pullout torque typically falls within 200-300% of the full-load torque. This class is suitable for general-purpose applications with relatively constant loads, such as fans, pumps, and machine tools, where high starting torque is not a primary requirement.
Squirrel cage motor Class B is designed for reduced starting current while preserving standard starting torque. Characterized by low slip typically less than 5%. These motors are often used in applications where limiting the starting current is important to mitigate excessive voltage drops within the power system. This consideration is particularly relevant in contexts with limited power supply capacity or when sensitive equipment shares the same electrical network.
Squirrel cage motor Class C delivers high starting torque in conjunction with low starting current. This class finds application in scenarios requiring elevated torque during startup, such as conveyors, crushers, and heavy-duty industrial equipment. The high starting torque enables the motor to effectively overcome the inherent inertia of the load, while the concurrently low starting current minimizes disturbances to the power system.
Squirrel cage motor Class D provides exceptionally high starting torque, with high slip typically between 5% and 13%. This attribute makes them suitable for applications involving high-inertia loads that require a significant initial force to initiate motion, such as punch presses and shears. The high slip allows the motor to generate substantial torque at low speeds, a prerequisite for rapid load acceleration.
The IEC also maintains a comparable classification system, but with more granular categories and specific performance criteria. Both NEMA and IEC classifications serve as valuable resources for engineers and end-users in the selection of motors tailored to their unique operational requirements.